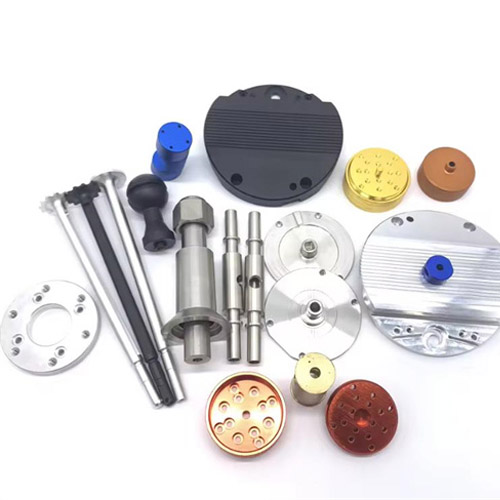
CNC Milling
CNC Milling is a subtractive manufacturing process that uses computerized controls and rotating multi-point cutting tools to remove material from a workpiece. Unlike CNC turning, where the workpiece rotates, in CNC milling, the workpiece remains stationary while the cutting tool moves along multiple axes to create complex shapes, slots, holes, and contours. CNC milling is highly versatile and capable of producing parts with intricate geometries and tight tolerances. The main working principle of CNC Milling is to use a rotating cylindrical cutting head and multiple chip groove milling cutters (usually referred to as end mills), which move along different axes, to process prismatic parts such as narrow spaces, grooves, outer profiles, etc.
CNC Milling is a type of milling machine that is controlled by digital signals from an electronic meter. It is an automatic processing equipment developed on the basis of general milling machines, with similar processing techniques and structures. CNC milling machines are divided into two categories: those without tool libraries and those with tool libraries, among which CNC milling machines with tool libraries are also known as machining centers.
Key Features of CNC Milling:
High Precision: CNC milling can achieve tolerances within micrometers, ensuring high accuracy in the final product.
Versatility: The process can create a wide range of shapes, including flat surfaces, slots, pockets, and 3D contours.
Multi-Axis Capability: CNC milling machines can operate on 3, 4, or 5 axes, allowing for the production of highly complex parts.
Material Flexibility: CNC milling can work with metals (e.g., aluminum, steel, titanium), plastics, and composites.
Repeatability: Once programmed, CNC milling machines can produce identical parts consistently, ensuring uniformity in mass production.
Common CNC Milling Operations:
Face Milling: Creating a flat surface on the face of the workpiece.
Peripheral Milling: Cutting along the edges of the workpiece to create contours or profiles.
Drilling: Creating holes in the workpiece.
Pocket Milling: Removing material to create pockets or cavities in the workpiece.
3D Contouring: Creating complex 3D shapes and surfaces.
Applications of CNC Milling:
Electronics
In the electronics industry, CNC milling is used to produce small, high-precision components such as circuit boards, connectors, and enclosures. These parts are critical for the functionality and reliability of electronic devices.
Application Examples:
Circuit Boards: CNC milling is used to create precise traces and holes in printed circuit boards (PCBs).
Connectors: Precision-milled connectors ensure reliable electrical connections in electronic circuits.
Enclosures: CNC-milled enclosures protect sensitive electronic components and ensure proper alignment.
Medical Devices
In the medical device industry, CNC milling is essential for manufacturing high-precision components such as surgical instruments, implants, and diagnostic equipment. The process ensures compliance with strict regulatory standards and delivers parts with exceptional accuracy and surface finish.
Application Examples:
Surgical Instruments: CNC-milled components for scalpels, forceps, and other tools ensure precise dimensions and smooth surfaces.
Implants: Custom-milled implants, such as orthopedic screws and dental prosthetics, are tailored to individual patient needs.
Diagnostic Equipment: CNC-milled parts for MRI machines, X-ray systems, and ultrasound devices ensure reliable performance.
Hardware Tools
In the hardware tools industry, CNC milling is used to manufacture high-precision components such as wrenches, pliers, and drill bits. These parts require high accuracy and durability to ensure the performance and safety of tools.
Application Examples:
Wrenches: CNC-milled wrenches provide precise and reliable tightening and loosening of bolts and nuts.
Pliers: Precision-milled pliers ensure accurate and durable performance in various applications.
Drill Bits: CNC-milled drill bits provide precise and efficient drilling in various materials.
Sports Goods
In the sports goods industry, CNC milling is used to manufacture high-performance components for equipment such as bicycles, golf clubs, and fitness machines. The process enables the production of lightweight, durable, and precise parts.
Application Examples:
Bicycle Components: CNC-milled parts like cranks, derailleurs, and brake components enhance the performance and durability of bicycles.
Golf Clubs: Precision-milled club heads and shafts improve accuracy and performance.
Fitness Equipment: CNC-milled parts for treadmills, weight machines, and other fitness equipment ensure durability and smooth operation.
CNC milling is a critical manufacturing process that offers high precision, efficiency, and versatility. Its applications span across industries such as electronics, medical devices, hardware tools, and sports goods, where high-quality, custom-designed parts with complex geometries are essential. By leveraging CNC milling, manufacturers can produce intricate and precise components with tight tolerances, ensuring optimal performance and reliability in their products.