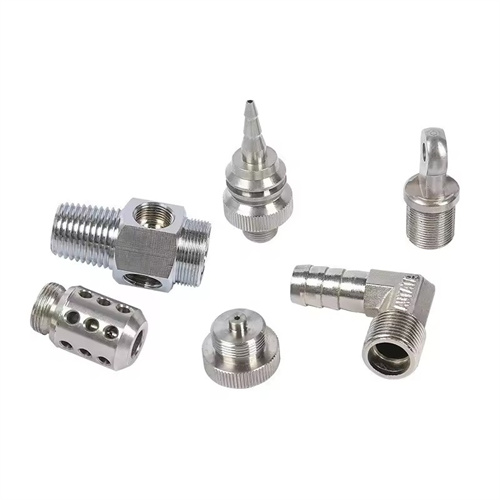
CNC Machining Ball Joints
Ball Joints are mechanical connectors typically used to link two or more components, allowing them to rotate freely in multiple directions. A ball joint consists of a ball head and a socket, enabling the ball head to rotate freely within the socket, thus providing multi-directional movement. This design makes ball joints highly useful in mechanical systems that require flexible motion and precise control.
Key Features of Ball Joints
Multi-Directional Movement: Ball joints allow rotation and swiveling in multiple directions, making them suitable for complex motion requirements.
High Load Capacity: Well-designed ball joints can withstand heavy loads, making them ideal for heavy-duty machinery and equipment.
Durability: Typically made from high-strength materials, ball joints have a long service life.
Precise Control: Ball joints provide accurate motion control, making them suitable for high-precision applications.
Ball joints have the following characteristics:
Multi directional mobility: Ball and socket joints allow connectors to move freely in multiple directions, as their design allows one spherical part to rotate freely within another spherical or hemispherical part. This makes them very suitable for applications that require multi-directional flexibility.
Strong load-bearing capacity: The ball joint can withstand forces and moments from multiple directions, as the spherical part can evenly distribute loads within the ball joint. This design allows the ball joint to maintain stable performance even under heavy loads.
Compact design: Compared to other types of joints, ball and socket joints usually have a more compact design, which makes them particularly useful in space limited applications.
Manufacturing Processes of Ball Joints
CNC Machining: High-precision machining using CNC machines ensures accurate dimensions and shapes of ball joints.
CNC Turning: Used to machine the spherical part of the ball joint, ensuring a smooth surface and precise dimensions.
CNC Milling: Used to machine the socket and other complex-shaped components.
The use of CNC machining lathes (also known as CNC lathes or CNC turning centers) to produce ball joints is an efficient and accurate manufacturing method. CNC lathes automatically perform various turning operations through computer control, thereby producing Ball Joints that meet design requirements. The following are the general steps for producing Ball Joints using a CNC lathe:
Design and Programming: Firstly, designers will use CAD (Computer Aided Design) software to create a 3D model of ball joints. Then, this model will be converted into code that CAM (Computer Aided Manufacturing) software can understand, usually G code or M code, which contains all the instructions and parameters that the machine tool needs to execute during the machining process.
Material preparation: Select suitable materials based on the design. For Ball Joints, factors such as wear resistance, strength, and toughness may need to be considered.
Machine tool setting: Install and fix the workpiece on the CNC lathe. Meanwhile, select the appropriate cutting tool and install it on the machine tool.
Processing operation: Input the programmed G code into the control system of the machine tool, and start the machine tool for processing. The machine tool will automatically rotate the cutting tool according to the instructions in G code to remove excess material from the workpiece, thereby creating the shape of ball joints.
Processing inspection: After the processing is completed, perform quality inspection on Ball Joints. This may include size measurement, surface smoothness inspection, material hardness testing, etc. If non-conforming products are found, they may need to be repaired or reprocessed.
The advantages of CNC turning to produce Ball Joints include high precision, high efficiency, and high degree of automation. However, since CNC turning is mainly suitable for machining cylindrical workpieces, if the shape of ball joints are complex, it may be necessary to combine other CNC machining methods, such as CNC milling, etc.
Application Fields of Ball Joints
Ball joints are widely used in industries such as automotive, aerospace, industrial machinery, and medical devices. Below is an introduction to the applications of ball joints in four randomly
LED Lighting
In the LED lighting industry, ball joints are commonly used to adjust the angle and direction of light fixtures. For example, in adjustable LED lamps, ball joints allow users to direct the light as needed, achieving optimal lighting effects. The multi-directional movement capability of ball joints enables lamps to adapt flexibly to various lighting requirements.
Application Scenarios:
Adjustable LED Lamps: Used in residential, office, and commercial lighting systems.
Stage Lighting: In theaters and performance venues, ball joints are used to adjust the angle and direction of lights to create different lighting effects.
Construction
In the construction industry, ball joints are often used in heavy machinery and equipment, such as cranes, excavators, and concrete pump trucks. These machines require flexible movement in multiple directions to adapt to complex construction environments. The high load capacity and durability of ball joints make them an ideal choice for such equipment.
Application Scenarios:
Cranes: Used to connect the boom and base, allowing the boom to move flexibly in multiple directions.
Excavators: Used to connect the excavator arm and body, enabling multi-directional movement of the arm.
Concrete Pump Trucks: Used to connect the pumping arm and chassis, allowing flexible adjustment of the arm.
Toys
In the toy industry, ball joints are commonly used in action figures and model toys. These toys require flexible movement in multiple directions to enhance playability and fun. The precise control offered by ball joints enables realistic movements and poses in toys.
Application Scenarios:
Action Figures: Such as action dolls and robot toys, where ball joints are used to connect limbs and torsos, enabling multi-directional movement.
Model Toys: Such as car models and airplane models, where ball joints are used to connect wheels, wings, and other parts, allowing flexible movement and adjustment.
Medical Devices
In the medical device industry, ball joints are often used in surgical instruments, rehabilitation equipment, and diagnostic devices. These devices require flexible movement in multiple directions to achieve precise operations and diagnostics. The high precision and durability of ball joints make them an ideal choice for such equipment.
Application Scenarios:
Surgical Instruments: Such as endoscopes and surgical clamps, where ball joints are used to connect various parts of the instrument, enabling precise operations.
Rehabilitation Equipment: Such as prosthetics and rehabilitation robots, where ball joints are used to connect joints in prosthetics, enabling flexible movement.
Diagnostic Devices: Such as ultrasound probes and X-ray machines, where ball joints are used to adjust the position and angle of probes for accurate diagnostics.
As a multi-directional mechanical connector, ball joints have extensive applications across various industries. Whether in LED lighting, construction, toys, or medical devices, ball joints play a crucial role by providing flexible movement and precise control. Through CNC machining technology, the manufacturing precision and durability of ball joints have been significantly enhanced, meeting the demand for high-quality mechanical components in various industries.